The Algorithm that Transformed Warehouse Chaos
Reduced shipment prep time by 70%, improved accuracy to 95%, and cut costs by 40%. Five years later, it's still the company's operational backbone.
It started with a call from a friend of a friend — the owner of a logistics company drowning in spreadsheets and manual processes.
“We spend hours matching products to shipments," he explained. "My warehouse staff is burning out comparing Excel files to physical boxes."
His company imported products in bulk – entire trucks filled with hundreds of boxes – then redistributed them in smaller packages to clients.
The complexity was staggering: thousands of Excel rows representing individual products spread across hundreds of physical boxes.
The Excel Nightmare
Each incoming shipment arrived with a massive Excel document – often thousands of rows long. Each row represented a single product with 10-15 different attributes, essentially a database dumped into Excel.
Warehouse staff would manually compare this spreadsheet to physical boxes, trying to match products to outgoing shipments. A person might spend hours figuring out which boxes to open for a single shipment.
Why it matters: With hundreds of boxes and thousands of products, even experts made costly mistakes. One wrong product meant unhappy clients and expensive returns.
First Step: Taming the Data Beast
We built an import system that could parse these massive Excel files into a virtual warehouse.
The key insight: only 3-4 attributes actually mattered for distinguishing products. We created custom grouping rules that dramatically simplified the data while preserving essential distinctions.
Now, instead of thousands of indecipherable rows, we had a clean virtual inventory – but the hardest part remained.


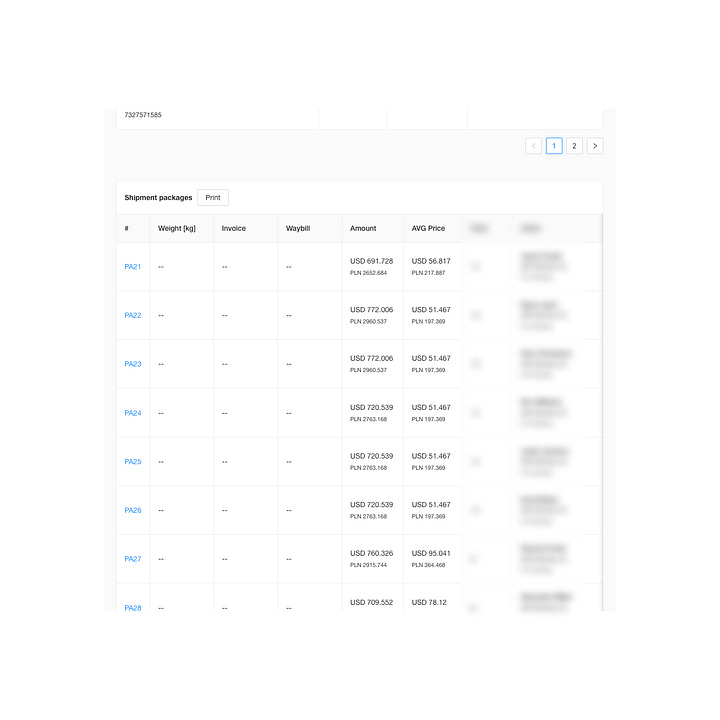
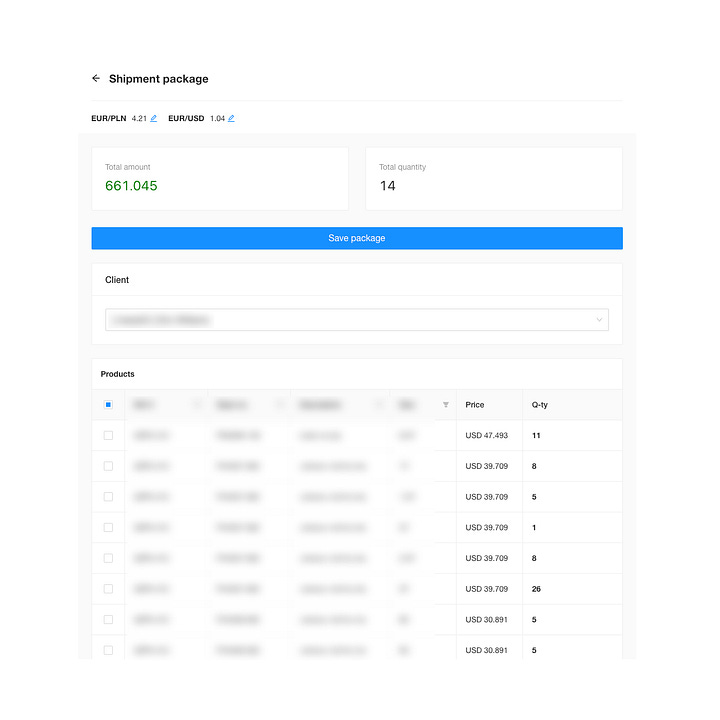
The Real Challenge: Human Exhaustion
With digital import working, we mapped the entire workflow: creating shipments, assigning packages to clients, calculating weights and costs, even generating documentation
But standing in the warehouse, I watched a staff member squint at a box label, check a printed Excel spreadsheet, walk to another aisle, open a box, take two items, then repeat this process dozens of times. It was meticulous, exhausting work comparing tiny numbers on boxes with endless rows on paper.
The core problem was clear:
The decision problem: Which boxes should I open? Which products should I take? How could we eliminate the mental burden of cross-referencing thousands of items?
The Algorithm: Our Breakthrough Moment
We created what we called "The Buffer" – a smart algorithm that:
Takes your shipment requirements
Evaluates all warehouse boxes against these requirements
Prioritizes boxes you don't even need to open – 100% matches for the shipment
For partially matching boxes, suggests what to take and what to leave
Generates a printable report for warehouse staff
The algorithm transformed hours of mental calculation into seconds of computer work. What once required expert knowledge now produced clear instructions for any worker.
Digital Tools: The Barcode Scanner
The next step toward modernization was obvious: replace printed spreadsheets with a digital barcode scanner. Each box already had a barcode that matched one of the columns in the Excel file.
When we implemented the scanner in the warehouse, we quickly discovered additional challenges:
The darkness problem: Warehouses were often dimly lit, making barcode scanning difficult.
The connectivity issue: Warehouse areas frequently had poor internet connections.
We enhanced our scanner with instant torch activation and aggressive caching – when a worker entered the warehouse, all the data came with them on their device, no internet required.
Paper Meets Digital: The Hybrid Approach
A surprising insight: many warehouse workers still preferred paper. Rather than fight this, we embraced it.
The system generated printable reports that workers could carry alongside their mobile app. Scan a box, and both digital and paper tools would tell them what to do:
Take the entire box: It perfectly matches shipment needs
Take specific items: For partially matching boxes
Leave it alone: Not needed for this shipment
The Results: From Hours to Seconds
The impact was immediate:
Buffer generation: From hours to seconds
Shipment preparation time: 70% reduction
Box selection accuracy: 95% (up from ~70%)
Operational costs: 40% decrease
The warehouse manager put it simply:
“Before, only our most experienced staff could build efficient shipments. Now anyone can do it and do it better.”
The Lasting Impact
What started in 2020 has evolved into the company's core operational system. Five years later, they're still using it daily, with ongoing improvements like multi-currency support, margin calculations, and automated documentation generation.
The lesson? Sometimes, the most impactful innovation isn't flashy technology — it's applying smart algorithms to solve real human problems.
We created a system that whispers to boxes, telling workers exactly where to find what they need, transforming warehouse chaos into orchestrated efficiency.